|
|
i-Fork AGV
|
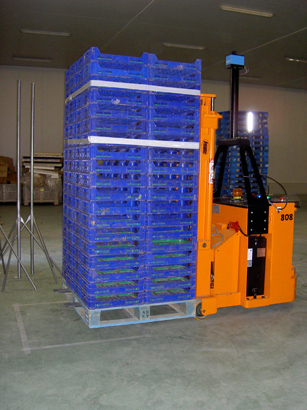 |
|
The i-Fork AGV is based on a custom modified OMG 808 fork-lift truck,
which included electrically assisted steering mechanism. This truck
is able to carry loads of up to 800 Kg , lift them upto 3.1 m of height,
and reach a linear top speed of 2.0 m/s. A series of custom microcontroller-based
boards are in charge of the low level control of the elevation, traction,
and direction motors. All of them are connected to the main CPU by
way of a CAN bus, operating at 1 Mbs. The AGV includes a SICK laser
based positioning unit and a SICK laser scanner sensor linked through
serial ports to the main CPU. Additionally, the platform has two security
switches to stop the vehicle in case of failure, and a switch to change
from manual to automatic mode. |
|
|
|
The main CPU runs all the control software, which is
based on a two layer hybrid architecture. It is worth noting here
that all the software has been written in the Java programming language.
The upper layer runs the navigation and planning modules. The first
one updates the different grid maps from processed sensor readings
while the second one generates plans and monitors the execution of
them. The lower layer runs the perception module, in charge of processing
sensor data, and the behaviour based controller, which performs the
actual tasks, mostly path-following controllers. |
|
|
|
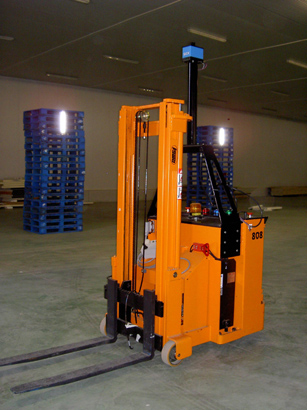 |
|
Additionally, there is an operator interface on a remote machine,
which is linked through a wireless ethernet network. This interface
allows the operator know the current position of the AGV and the part
of the plan that is currently executing. Moreover, at any time the
operator can send a new task to the AGV. This software allows the
operator changing or adding relevant places of the environment, such
as adding a new docking place, and then sending the new map to the
AGV. |
|
|
|
One of the main advantages of the iFork system is the flexibility
in defining the plant of the operation areas. While in typical systems
modifications of the layout imply halting the system, our system
allows for modifications in real time. Moreover, only a minimal
amount of information is required for defining the plant, as location
of docking places, doors or passageways and waypoints for docking/undocking
operations. There is no need of an accurate model of the different
walls an obstacles. In fact, if new obstacles appear, the iFork
system incorporates this information into its own maps. All this
flexibility is because there are no predefined paths. The robot
computes continuously the way to get to the desired point. The interface
to an intelligent warehouse planner/manager is very simple. The
manager just have to provide a list of docking/undocking operations.
The iFork system comes with its own production manager to automatically
generate orders to the robots, although it is not required.
|
|
|
|
|
 |